

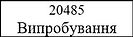

Leak test
The tightness control of products using penetrating substances is widely used in many industries. The testing methodology varies depending on the type of penetrating substances, the purpose and scope of the equipment, etc.
Test methods in which the substance used penetrates through unpressurized parts with a positive pressure drop is called compression, with a negative pressure - vacuum.
Testing and certification center "Yugtest" offers its services in conducting leak tests, both in Dniepro and in any other city of Ukraine.
Test methods

Hydraulic

Chemical

Capillary

Halogen

Bubble
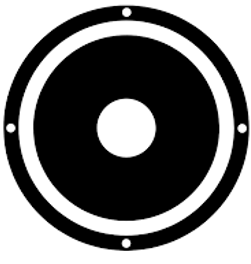
Acoustic
other
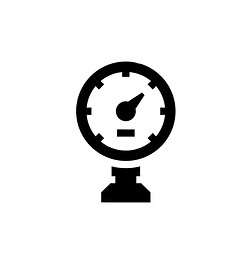
Manometric
The choice of method depends on its sensitivity, performance, cost, safety.
The leak test is carried out on products that for a certain time must maintain the necessary pressure of the working substance or leakage of which is strictly regulated. These values are indicated in the technical specifications. Products that must be tested for leaks include: tanks, gas pipelines, pipelines, valves, tanks, reactors, hydraulic systems, etc.
Leakages can be caused by various leaks in the materials from which parts and assemblies are made. The necessary tightness indicators are achieved by improving the designs, assembly processes, etc. The tightness requirements for vessels under excessive pressure are presented based on their volume, the norms of pressure change over a certain period of time.
Testing of vacuum systems should be carried out taking into account false leakage, which is not a consequence of loss of tightness, but prevents the preservation of the required degree of vacuum. Leakage can occur due to gas evolution from solids or internal leaks, which are channels connecting a closed tank with an evacuated volume, the formation of which occurred during manufacture and containing gas.
Causes of leakage
Tightness is a prerequisite for maintaining the operability of many products, so close attention must be paid to its control.
The leakage may be due to the following reasons:
-
the transformation of non-through defects into end-to-end due to various physical and mechanical effects;
-
Shell deformation as a result of mechanical or thermal influences;
-
Temporary overlap of leaks due to ingress of dirt, liquids.